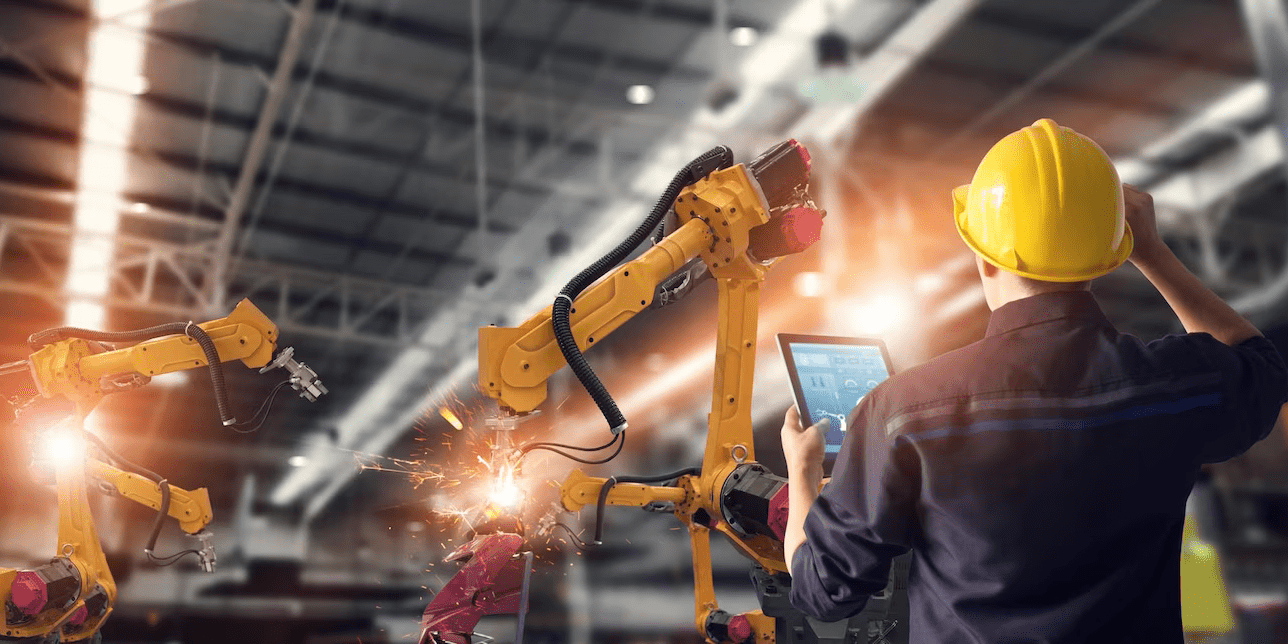
Digital manufacturing solutions are shaping the future of productivity in the manufacturing industry. ERP solutions have emerged as the preferred choice, with 47% of companies actively seeking ERP systems manufacturers [1]. As manufacturers often face issues such as lowered productivity, excessive energy wastage, and industrial hygiene management, SAP S/4HANA offers various manufacturing features to help companies:
- Reduce system downtime;
- Promote sustainability and energy efficiency, and;
- Create a safe environment for employees.
Downtime-free, uptime only
Enterprises in the manufacturing industry have been grappling with the recurring problem of unplanned downtime, as research reveals that approximately 82% of businesses have encountered unplanned downtime to varying degrees in recent years. This issue becomes more concerning, considering these episodes can endure at least four hours each, potentially leading to a staggering 800 hours of downtime annually [2]. Unplanned downtime is a major issue for manufacturing companies, with an estimated annual loss of $300 million [3]. This problem can be especially detrimental to small and medium-sized firms, as they often lack the resources to address these issues without external assistance.
To tackle this issue and improve efficiency and productivity, SAP Overall Equipment Effectiveness (OEE) offers a comprehensive set of capabilities. This SAP feature continuously collects real-time operational logs and performance data by leveraging an IoT network. The IoT solution analyzes this data through advanced analytics to provide insights into machine performance, enabling predictions of potential issues and enhancing overall efficiency. For instance, abnormal levels of vibration or heat from a piece of equipment can be detected, signaling a potential malfunction. This information can be quickly relayed to the operator and maintenance team, enabling them to address the issue before it escalates.
Additionally, SAP OEE harnesses the power of AI and machine learning algorithms to extract valuable insights and predict maintenance needs using sensor data. Studies have shown that predictive maintenance can reduce machine downtime by 30% to 50% and extend machine life by 20% to 40% [4]. Operators and managers can proactively identify issues, plan for repairs during periods of minimal impact on operations, and implement necessary corrective measures. Moreover, AI-powered tools can optimize processes and improve customer service by analyzing production line data, such as temperature, pressure, and flow rates, to identify opportunities for enhancement. By implementing predictive maintenance, manufacturing plants can avoid costly mechanical breakdowns, increase equipment uptime, and boost overall productivity.
Sustainability takes the center stage
With increased energy consumption, efficient energy management has become a critical factor for success in modern manufacturing operations to reserve energy and reduce waste. Hence, ESG (Environmental, Social, and Governance) has emerged as a vital focus point for businesses, encompassing strategies that address environmental sustainability, social responsibility, and effective governance. This comprehensive approach not only contributes to the long-term sustainability and success of companies but also aligns them with the growing expectations of stakeholders, investors, and the wider society. Specifically, ESG-focused institutional investment is projected to surge by 84% to reach a staggering US$33.9 trillion by 2026 [5]. This remarkable growth signifies a substantial increase in businesses' willingness to embrace sustainability and take proactive measures towards environmental, social, and governance factors.
With SAP Energy Management, manufacturers can unlock several benefits, including monitoring usage patterns, predicting energy demand, and optimizing energy consumption. By leveraging advanced analytics and automation capabilities, SAP OEE enables manufacturers to optimize energy usage and minimize wastage across the entire production process. Real-time monitoring and predictive analytics allow manufacturers to pinpoint energy-intensive areas, paving the way for targeted improvement strategies.
Furthermore, SAP Energy Management can simplify the monitoring and analysis of energy resources across various dimensions of the plant information catalog. Recognizing the crucial role of energy efficiency, enterprises can reduce up to 44% of carbon reductions by 2040 [6]. Not just carbon emissions but such comprehensive energy programs can potentially mitigate up to 1.1 gigatons of greenhouse gas emissions annually [7]. In addition to providing a solid foundation for carbon reduction strategies, this SAP solution helps companies organize and manage their energy resources. This allows them to more effectively track usage and cost data across various facilities, as well as monitor activity on an ongoing basis.
Safeguarding workplace from potential hazards
The manufacturing industry is a dynamic and bustling sector that is not without its fair share of challenges. The employees within this industry are no exception, as they are constantly exposed to various substances that can wreak havoc on their health and well-being. According to the U.S. Bureau of Labour Statistics, 373,000 nonfatal injuries and illnesses were reported within the manufacturing industry in 2020, with 340 fatal occurrences [8].
Neglecting to implement effective monitoring and upholding industrial hygiene principles can have severe consequences. Firstly, productivity could take a hit, directly impacting its overall profitability. The financial toll of employee health issues on employers is substantial, amounting to a staggering loss of 1.4 billion workdays and an astonishing USD 530 billion in revenue [9]. Nonetheless, if the company demonstrates its commitment to the well-being and welfare of its workforce, it contributes to the "S" aspect of ESG that is focused on social responsibility. Ensuring a safe working environment protects employees from physical and psychological harm, reduces the risk of accidents and injuries, and promotes a culture of care and responsibility. Additionally, it enhances employee morale, productivity, and retention, which positively impacts the company's overall performance and reputation. Mercer's research revealed that employers with high ESG scores not only achieve a 14% higher employee satisfaction rate but are also 25% more appealing to prospective talent than the average [8].
Therefore, SAP EHS (Environment, Health, and Safety) is a solution in SAP S/4HANA for enterprises to achieve industrial hygiene. With SAP EHS, organizations can attain real-time situational awareness across their entire enterprise, effectively mitigating noncompliance risks. This helps them foster a proactive safety culture, make informed decisions and take prompt action. Furthermore, SAP EHS facilitates the creation of a safer workplace environment by proactively addressing risks, hazards, and exposures. Specifically, manufacturers can enable efficient planning and scheduling of material movement, storage, and usage with Chemical management features. Manufacturers can effectively organize and coordinate the logistics of chemicals, ensuring they are available when needed and in appropriate quantities. Additionally, these features facilitate the creation of a comprehensive list of chemicals employed in manufacturing, providing visibility and control over the substances used. This solution also enables incident tracking, change requests, and the cultivation of a safety-conscious culture that prioritizes the well-being of employees and mitigates potential incidents.
Empowering a smart manufacturing future
In the ever-evolving manufacturing industry landscape, SAP S/4HANA rises above to become one of the most advanced solutions. Manufacturers can use these innovative solutions to leverage real-time data insights, predictive analytics, and intelligent automation to make informed decisions and identify bottlenecks.
With digital manufacturing solutions at the helm, manufacturers can embrace a new era of productivity with SAP S/4HANA, characterized by increased agility, responsiveness, and competitive advantage in an ever-changing global marketplace. By examining these manufacturing issues within the broader context of business operations, manufacturers can understand and resolve them as they occur. This ultimately leads to reduced downtime, higher-quality products, and increased operational efficiency.